The name “no clean flux”, “low solids flux”, or “low activated flux” suggests that these flux residues do not need to be removed because they are harmless to the end product. However, this is not quite correct! No-clean flux is actually only developed for mechanical soldering (wave, reflow, selective soldering). By machine soldering, the flux is fully activated during the preheat phase and the flux residues that remain after soldering are harmless to the end product. However, if the printed circuit board has to be coated after soldering, this no-clean flux residue can ensure that the conformal coating layer does not adhere properly to the printed circuit board surface. And that is why it is important that these flux residues are removed.
Note: even if the printed circuit board does not need to be coated, some no-clean flux residues can cause short circuits……..but why is it called “No-Clean Flux”?
Especially when hand soldering and rework using external flux that is added to the printed circuit board, you have to remove the flux residue after soldering because you don’t know exactly how long you have to heat. If not all activators in the flux are fully activated (if the activation temperature has not been reached) then the flux residues are still active and this means that a short circuit (due to electromigration/leakage current) can occur afterwards due to moisture.
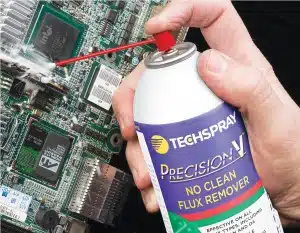
No Clean Flux remover
What is the best way to remove no-clean flux residues?
The flux supplier can provide the answer to this question. Depending on which type of no-clean flux, he knows what is best for cleaning. There are 24 different types of flux (see J-STD-004). Water-soluble flux can be cleaned with water and soap. Alcohol-based flux is better cleaned with isopropanol (IPA). There are special flux removers that have been specially developed for the removal of no-clean flux residues. Always read the safety precautions before using these toxic chemicals!!! Provide good ventilation and work with safety glasses if possible.
How to clean manually:
- Read the safety instructions
- Spray the flux remover on the surface to be cleaned
- Brush the cleaning fluid back and forth
- Remove the residue with an ESD-safe cloth
You can also spray the flux remover directly into the ESD-safe cloth so that all residues are absorbed:
Further information about cleaning can be found in IPC-7711/7721 and IPC-CH-65.
After cleaning, for example, flexible printed circuit boards and other sensitive printed circuit board materials and/or moisture-sensitive components, they have to be dried in an oven.
How do you know if you have cleaned properly?
There are several test methods to determine this. For example, the SIR test (Surface Insulation Resistance Test), which measures whether a short circuit is caused by the flux residues left behind.
Further information on printed circuit board cleanliness testing can be found in J-STD-001 and IPC-TM-650.
Example of a ROSE tester (ROSE = Resistance Of Solvent Extract) for measuring the purity after cleaning No-Clean flux residues. It measures the last remaining ionic residues. Ionic residues are e.g. Sodium (Na), Chlorine (Cl), Bromine (Br) and Fluorine (F). These ionic residues, in combination with moisture, can cause dendritic growth (electromigration/short circuit).
And that’s why you have to remove these no-clean flux residues.
Other methods to find back flux residues (optically) can be found on the Zestron website (www.zestron.com), Zestron Flux test, Zestron Resin test.
Conclusion:
When hand soldering, you should always clean no-clean flux residues, regardless of which flux you use.
When soldering by machine, you only have to clean no-clean flux residues if the circuit board still needs to be coated.