During the immersion, wave or selective soldering processes and in the HASL finish application processes, metals will dissolve in the liquid solder. The degree of dissolution depends on the base materials used (finishes on tracks and component leads/metallization’s), solder composition (e.g. the SAC alloy will dissolve copper faster than SnCu), process temperature and process time.
In the IPC documents IPC/J-STD-001, IPC/WHMA-A-620 and IPC-6012 you will find tables with limits for the maximum contamination values of solder baths, as they are used in wave soldering processes and small tin baths/fountains/pots for the tinning of wires. If you carry out these types of processes and the aforementioned IPC documents are mentioned in your contracts with your customers, you must regularly test your baths for this contamination (or have them tested). You must determine an interval for these analyses that you must also record and adhere to in your process documentation. A method for determining an interval based on solder consumption and usage hours per month can be found in the graph below. The German organization DVS (Deutscher Verband für Schweißen und verwandte Verfahren e.V.) recommends doubling the interval during the first 3 months if the solder composition in the bath has been changed.
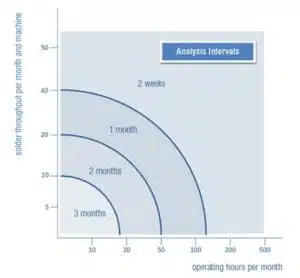
Graph for determining the analysis interval as suggested by DVS.
And if your customer wants to perform an audit at your place, you must certainly ensure that you can also show the reports of all analyses, of all baths in the past year, after all this is also a requirement of IPC.
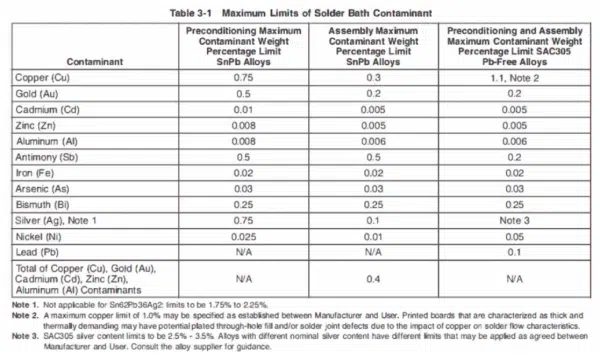
Table from IPC/J-STD-001 with the maximum contamination limits for different elements in the solder bath, the table in the IPC/WHMA-A-620 is comparable, IPC-6012E only gives values for SnPb comparable to the assembly column above.
If you use other lead-free alloys than the SAC305 mentioned in the table, other limits would apply, but these are not given by IPC. In general, however, your brazing alloy supplier can advise you on the limits for the alloy used. The German organization DVS has also published a publication with a table for alternative alloys.
How to perform the analysis of your baths?
If you have the knowledge and equipment, for example to carry out a spectroscopic analysis, you can of course perform this yourself on a regular basis. If you cannot do this internally, you will have to have it done by an external laboratory. Your soldering alloy supplier can also do this for you. Depending on the amount of solder purchased annually, some will even do this free of charge or charge only a small fee. For this, a standard mold is often used to take a sample from the bath and send it to you. It is recommended to increase the temperature of the bath by 10 degrees when taking the sample.
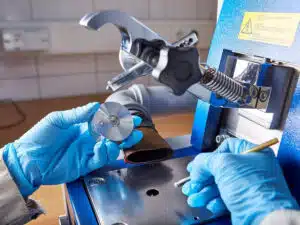
Determining the contamination using spectroscopy, the sample is in a special mold.
What if I don’t want or can’t do an analysis. Is there an alternative?
IPC indicates that a (complete or partial) replacement of the contents of the solder bath is also possible as an alternative. This will be a better alternative, especially for small solder baths (solder pots), which are used for tinning wires. However, you must also define an interval for this. A customer might ask you for an audit based on which you have established the replacement intervals to ensure that no excessive contamination occurs.
What can happen if there is still too much pollution?
That depends on which substances are in excess in your alloy. Below you will find an overview of a number of listed substances, some properties and their influence on the performance of the solder joint, if the concentration exceeds the limits.
Conclusion
Although IPC prescribes that you should regularly analyse your solder baths, it is also in your own interest as an electronics manufacturer to do this. Elevated concentrations can cause problems with solder joint reliability or introduce other problems.